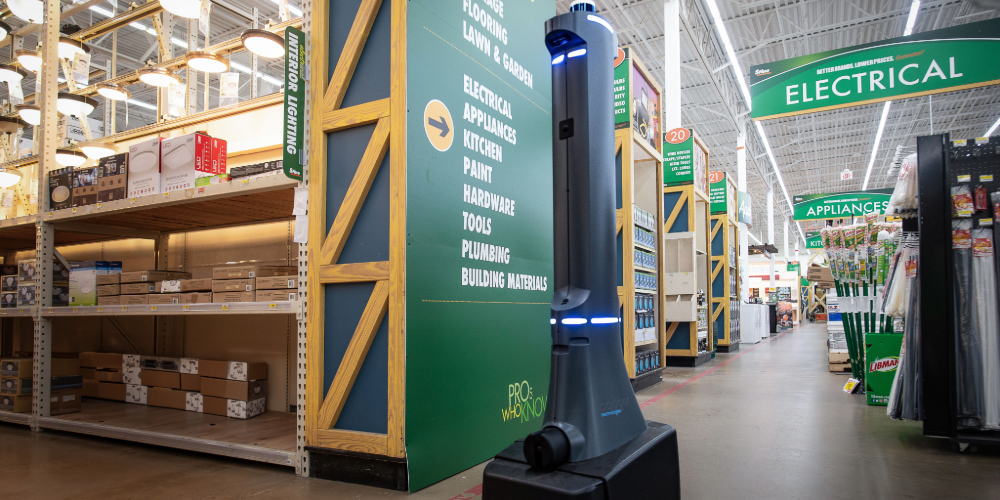
Autonomous Robots Foster Employee Efficiency
In an effort to improve employee efficiency and enhance the operation, several independent home improvement retailers have implemented autonomous robots as part of its technology strategy.
We continually seek innovative ways to elevate customer service while removing operational obstacles for store associates.
- Waylon Walker
Senior vice president, operations and merchandising for McCoy’s
The robots free our associates from time-consuming inventory checks, enabling them to help customers while ensuring our products are placed and priced correctly.
- Robert Spears
CIO for Stine Lumber
As the company strives to elevate customer service and improve on-shelf availability and the price integrity of its products, McCoy’s Building Supply has partnered with Badger Technologies to bring autonomous robots into stores.
After a successful pilot of five robots, the operation, which has 85 locations in New Mexico, Oklahoma and Texas, will be adding the robots to five additional stores. David Paul Strom, McCoy’s director of loss prevention and operations support, says the company plans to expand the robot fleet even more next year.
“While I initially thought we might be stepping out a bit too far, I soon realized that this was well within our wheelhouse and a good fit for us,” Strom says. “We are discovering new ways to utilize the data Randy—which we affectionately named the robot—provides in the store and in the supply chain.”
The autonomous robots roam the aisles of the store and provide daily updates on the availability and pricing of up to 50,000 SKUs per location. They are able to detect out-of-stock and incorrectly priced products with more than 95% accuracy. Since implementing the technology, McCoy’s has decreased out-of-stock products by up to 50% and improved price tag accuracy by more than 97%.
“We continually seek innovative ways to elevate customer service while removing operational obstacles for store associates,” says Waylon Walker, senior vice president, operations and merchandising for McCoy’s. “With Badger Technologies robots, we can eliminate manual, time-consuming inventory checks and attain real-time data to better address customer preferences and buying trends.”
Along with providing a higher level of customer service, the robots have also increased employee efficiency. The robots can complete inventory shelf scans in just two hours a day, a task that previously took employees 50 hours a week, a 72% reduction in time.
“Our employees, especially those with zoning, salesfloor and inventory management responsibilities, love the robots,” Strom says.
Additionally, the multipurpose, autonomous robots keep track of product locations, which can speed restocking the most popular products while assisting stores with merchandise forecasting, commodity management and planogram compliance.
“The robots make life easier for everyone by identifying opportunities to fill empty pegs,” Strom says. “Rather than having to scan all the aisles to find and fix problems, employees can access the robot dashboard, which details the issues, provides pictures and details the exact aisle or location of each issue.”
Making Gains in Operational Productivity
As it works to improve efficiencies throughout its operation, Stine Lumber LLC has also rolled out autonomous robots from Badger Technologies. Currently, Badger Technologies multipurpose autonomous robots are in four of the 12 Stine locations in Louisiana, with plans to roll out more robots to additional locations in 2024.
Stine Lumber CIO Robert Spears says the decision to introduce autonomous robots was driven by the company’s overarching commitment to its hard-working associates and loyal customers.
“We always look for innovative ways to increase productivity by removing operational obstacles,” Spears says. “Badger Technologies’ robots free our associates from time-consuming inventory checks, enabling them to help customers while ensuring our products are placed and priced correctly.”
The company will be able to improve price tag accuracy by more than 97% with the multipurpose autonomous robots. The robots will also detect out-of-stock (OOS) products with more than 95% accuracy while helping to decrease OOS products by up to 50%.
Spears says they are also measuring the impact of the in-store robotics deployment in terms of gains in operational efficiencies and productivity through automating previously tedious tasks, such as manual shelf scans to ensure they are stocked with an optimal mix of products at the right prices.
“Because store associates are responsible for managing many different SKUs, the ability to automate these daily product inventory checks is empowering Stine employees to spend more time interacting directly with customers,” Spears says. “In terms of time savings, the robots are saving between 70-80 hours a week of time it would normally take store associates to complete shelf scans manually.”
Stine Lumber is always looking for ways to improve operational efficiencies, and the adoption of autonomous robots represents a major step forward for the organization, Spears says. The ability to have a “shelf-eye” view of the entire store offers a real-time snapshot of product inventory, enabling the company to prioritize product replenishment, as well as gather more timely insights into local buying patterns, customer preferences and relevant seasonal trends.
“Armed with up-to-the-minute shelf details, Stine can ensure ample supplies of the most popular products, even during peak shopping times,” Spears says. “Stine is taking full advantage of the data gathered daily by the robots to improve store operations, while enabling their associates to spend as much time as possible improving customer shopping experiences, which has long been the hallmark of the company’s success.”
The multipurpose robots also support store safety and cleanliness by identifying hazards, such as spills of liquids, powders or bulk-item foods, to further mitigate risk.
“Our multipurpose autonomous robots offer much-needed relief by extending staff operations and producing critical data to increase efficiencies and improve shopping experiences,” says William (BJ) Santiago, CEO of Badger Technologies. “The robots deployed by Stine are helping improve customer satisfaction, storewide operations and retail revenues.”